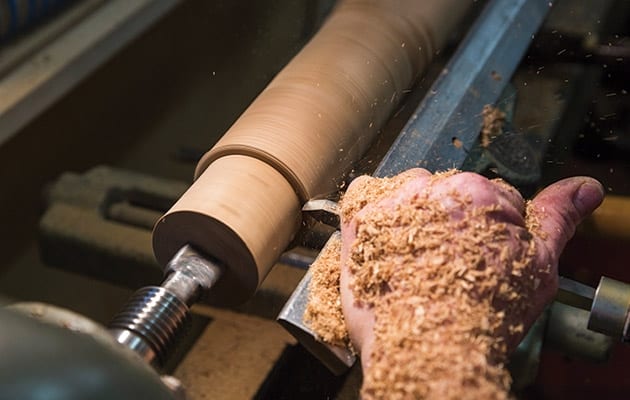
What does craftsmanship signify in an industry that’s overwhelmed by machinery? How do you define the relationship between craft and technology, and how can these apparently polarising methods continue to exist in harmony?
Founded by Terence Conran and Sean Sutcliffe over 30 years ago, Benchmark is a UK-based furniture brand that has continued to root itself in the value of craftsmanship. By finding the balance between technology and traditional techniques, not only has the company managed to succeed in keeping age-old skills alive in the process, it has also opened up a new dialogue as to what craftsmanship means today.
An example of this successful equilibrium can be seen in the form of the OVO furniture range which will be on display at this year’s 100% Design event in London. Designed by Foster + Partners in collaboration with Benchmark, the collection features two variants of dining table, benches, a sideboard, shelving unit, high table, stool and tables. It has been described as a celebration of craftsmanship, as each piece combines considered and smooth detailing with strong materiality.
The Benchmark HQ is set deep within rural woodland in Berkshire
Designed with a modest simplicity, its bold and tactile wooden frame irresistibly invites the sense of touch. It bellows with craft, yet this outcome is one that would not have been achieved if it weren’t for the technology.
That’s why it was paramount to go behind the scenes to see the inner workings at Benchmark. Nestled deep in the countryside at Kintbury in Berkshire, just an hour’s drive out of London, the studio, showroom and workshop house a team of highly skilled craftsmen and in-house designers who also collaborate externally on the growing portfolio of Benchmark furniture collections.
Tabletops are cut by CNC – now exchanged with a new machine
Upon arrival for the tour, the setting is idyllic; not only is the woodland a symbol of Benchmark’s primary material, but the vast landscape is replicated with its various workshop houses. We begin at the mill, where Sutcliffe tells me there are new machines being brought into the workshop – various employees are inputting the ventilation pipes and exchanging the old with the new as we walk by. It’s an upgrade, to say the least.
Pieces of the OVO range are assembled in the workshop
The mill is where the staff cut up bits of wood, reduce them down to size and create multiple tenon joints – it’s a loud and mechanical part of the workshop and one that not only encompasses new machinery, but the old systems too. We take a glance at one machine in particular – one that “cuts square holes” by means of “old-fashioned craftsmanship”. Yet Sutcliffe then recounts that “a lot of this process is what gets replaced by the CNC”.
Detailed woodworking is carried out by hand and machine
After some questioning as to how the choice is made to use the old or new machinery for a particular product – which leaves a small amount of time for pondering – it becomes clear that having these old processes is what in fact keeps traditional craft alive.
The OVO tabletops are cut by the CNC machine in the Benchmark mill
“If I took all that to the CNC, then the next generation who come through as apprentices wouldn’t even learn how to mortise and tenon stuff. So there’s a whole process that wouldn’t get taught,” says Sutcliffe. This implementation of technology is thus not a problematic transition, which leads him to reflect further: “I have a corny saying that states the best tools are our hands; our second best tool is a 5-axis CNC.”
Traditional craft tools are used alongside the modern machinery
The next stop is the upholstery room, planted rustically in an old barn-like building with vast wooden beams. As well as being dramatically tranquil in comparison to the sound-filled mill we have just visited, its interior is packed with various textiles and upcoming projects.
Skilled workers file down the surface of the OVO dining table
This peaceful rest continues in the main working area – also referred to as the “hand workshop”. Again, new machines are being fitted, and the space is vibrantly filled with around 28 people deep in work. “These guys are all at various levels of age and experience. Mickey’s been here a long time and is actually one of the machinists who works in the mill. He’s worked here for 28 years and first came as a 15-year-old and is now one of our senior hands. You’ll see a lot of apprentices… It’s where the great majority of people in here have come from. We have a queue of people waiting at our door to be apprentices.”
Fingerjointing detail on the drawers of the OVO oak sideboard
Before long, we enter the production room, where around 300 jobs have been logged on the wall charts, followed by the metal workshop, the polish room – with a “charming” recipe book of colours – and the outside wood waste area and silo.
“Half the wood we buy ends up out there – all the sanding dust, the sawdust, the splits, the sap wood and the shavings – and it’s about 50% wastage,” says Sutcliffe. “This deals with all the filtration; it goes into the silo and that’s our heating plant and our winter supply. It will accumulate all over the summer and that is what will keep us warm in the winter – we reuse all the energy.”
At the end of the tour, it’s clear that as well as grounding itself in sustainability, the Benchmark ethos is also rooted in revolutionising its processes to allow for the best possible practice. “The rules are constantly changing,” Sutcliffe says.
This includes ever-evolving technologies and keeping up with the market: “Things like the OVO, it’s intensely tactile and soft but that wouldn’t have happened in a more brutal male-dominated world of 20 years ago. That all informs the marketing, and we’re talking to a much more female-based audience.”
So in this sense, perhaps the new definition of craft encompasses the ever-changing, the feminine and the ability to retain the high level of skill that forms the backbone of what craftsmanship is today. And, it seems that Sutcliffe and his team are on the path to keeping up with the advancing industry – and the OVO collection is a skillful example of this.
OnOffice visits Benchmark’s workshop to see how traditional crafts and modern methods come together in its OVO range