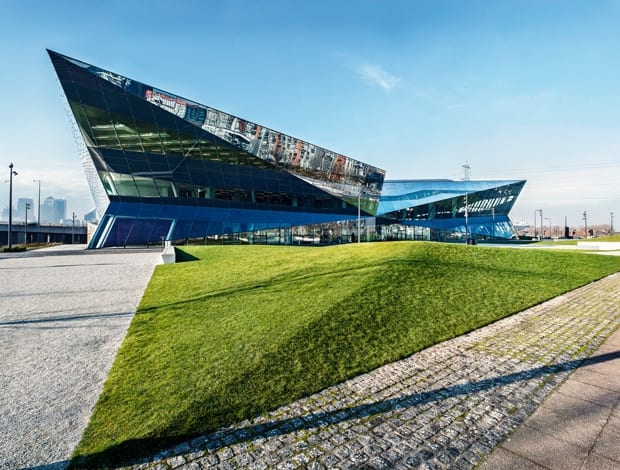
The proportion of the world that dwells in cities is set to rise from one half to two-thirds by 2050, and The Crystal, designed by Wilkinson Eyre Architects, is Siemens’ way of staking a claim on the management of this mighty demographic shift. Part exhibition space, part conference centre and part think-tank, the new Docklands building is the tech company’s showcase for its work in urban sustainability. Unsurprisingly, technology and active systems are at the heart of Siemens’ sustainability vision, and by making The Crystal only the first building in the world to achieve maximum credentials in both LEED and BREEAM, it is apparently sending a decisive message about the part that architecture can play in the coming transition.
Reviewing The Crystal is a balancing act between being fair to this technology-rich sustainability vision, and the fact that it is pioneering and exemplary in other respects. A “fabric first” approach is now advocated as a top priority for building design, rather than prioritising the sorts of active energy systems and technologies that Siemens manufactures. This is because a super-efficient fabric is vital for ensuring the long-term energy performance of a building, whatever it is fuelled by, especially considering that the building fabric will prevail far beyond the lifespan of most active technologies. And if a building’s energy demand is small, it is far easier (and cheaper) to meet the remaining energy via active low-carbon systems, whether provided on or off site. Equally, however, the embodied energy of renewables should not be neglected, because the greater the energy need, the greater the renewable energy array required, so even “clean” energy should never be “wasted”.
The Crystal’s passive design features include BMS managed natural ventilation and night cooling, BREEAM recommended minimum daylighting levels, winter solar gain, where desirable, and partial self-shading through the building form, which appears most effective for low autumn and spring sun. Heating and cooling account for 10% of energy consumption. Its air-tightness is four times better than the minimum building regulations requirement and the total designed energy needs are estimated at around 212 kWh/m2 per year, with 83 kWh/m2 year for the office and corporate area. Despite being mainly clad in glass, around 60% of the facade is opaque, and insulated with U-values of 0.23-0.16 W/m2K.
While The Crystal is designed to perform 40-50% better than similar buildings, some will argue that its fabric performance could have been pushed further still. However, as ARUP’s lead building services engineer Mark Plummer explains: “It is important to analyse where the energy is being lost, and target those areas. Our design-stage energy models showed that cooling, rather than heating, is predominant, and to further insulate the facade gave minimal energy-saving benefit considering the exponential increase in cost. It was more important from a technical point of view to limit solar gain, which we did by minimising transparent glass, tilting the glass away from the sun, and using high-performance solar glass.”
The choice of such a high-tech glass facade is striking architecturally, and partially reflects the building’s surroundings due to the stark angled geometry. “We wanted to challenge preconceptions of what ‘green’ architecture looks like, encapsulating the ambition of Siemens,” says Sebastien Ricard, lead architect at Wilkinson Eyre. “To achieve this, we used highly insulated and efficient glazing to create a lightweight structure that doesn’t look like other highly sustainable buildings.”
In this regard, The Crystal undoubtedly succeeds, but it is a trade-off with high embodied energy, reflected by lower material credits in LEED and BREEAM. The energy centre and a garden pavilion are timber-clad but there is an absence of timber in the main building – an omission further highlighted by one of the timber-clad internal exhibits, which advocates the material’s use in a sustainable urban context.
“The Crystal incorporates a structural frame specifically designed to reduce the amount of steel within the columns, thus reducing embodied energy,” Mark Plummer explains. “The tapering sections are sized to reflect the forces and therefore steel is only utilised where required. By maximising the amount of recycled content of materials used during the construction of the building, the embodied energy has been significantly reduced.” Such a material approach highlights that a life-cycle assessment analysis could have been employed to augment the sustainability strategy, without jeopardising the architectural design.
Give the decision to prioritise sustainable technologies in favour of a super-efficient building fabric, The Crystal has got a lot right. It is all-electric (not on the gas grid) and to design a building with the vision for it to be weaned of fossil fuels is an admirable commitment. The heating and cooling is supplied by a 17km network ground-source heat pump and nearly 1,600sq m of highly efficient solar PVs and 19sq m of solar thermal panels, to top up the heat pump’s hot water supply. To the credit of the client and design team, the technologies are all integrated rather than bolted on, although this does mean that the building has limited use as an educational tool in itself, aside from a few displays. The building is connected to the grid to export surplus energy and import it when needed, and only time will tell how this balances out once the year-on-year electricity consumption and production are published.
The Crystal received maximum water credits for both BREEAM and LEED, prioritising water-efficient appliances over active water-harvesting and reuse systems (these systems have a significant embodied energy and require energy to pump and chemically clean water). Rainwater is caught on its extensive roof, which is filtered and treated to supply 90% of the potable drinking water. Moreover, 100% of the wastewater, including black water, is chemically treated on site to flush toilets and irrigate the landscape. This innovative approach would not ordinarily be suitable for urban settings due to space and site constraints, and it also requires extra energy to operate.
Flood resilience is obviously crucial, as the area is adjacent to water reservoirs and rivers. The soft landscaping is inspirational and a welcome relief from the hard surfaces of the surrounding dock, though it feels a missed opportunity that this is not part of the building’s exhibit to showcase the benefits of nature in cities – instead there is an internal exhibit that includes a high-energy, high-maintenance living wall.
Finally, there is live monitoring of energy used and produced, which informs the client and users how to continuously and seasonally optimise technologies and building performance. The verdict is still out whether the building and its technologies will perform as modelled and predicted. The publishing of future planned Post Occupancy Evaluation (POE) and Building Performance Evaluation (BPE) will be an invaluable source of information and feedback for future building design.
The Crystal may have achieved its aim to become an iconic sustainability education centre and community hub, but it is unlikely to become a prototype of urban sustainability due to its cost (≈£4,000/m2). Its suburban location, combined with a technology-rich approach, allows it to achieve an “energy and water island” status. However, its unusual context has its drawbacks as it is not only difficult to replicate on tighter, more urban sites, but might also give the impression that this is what sustainable buildings are about, when more efficient buildings on a lower budget could be delivered.
The Crystal in numbers
– 67% of the concrete aggregate used in the building’s construction came from secondary sources (ie, waste material); 100% recycled steel was used for the building’s reinforcement, and the roof is made from 100% recycled aluminium
– Space heating and cooling is supplied by two ground-source heat pumps, which can simultaneously heat and cool
– 94% of the waste produced during construction was recycled
– IT and “small power” account for the majority of the building’s total energy output – 63% – while heating and cooling use 10%
– 1,580sq m of solar PV panels on the roof are predicted to generate 256MWh annually, around 17.5% of the building’s predicted (average) energy consumption; 19sq m of solar thermal panels are expected to generate a further 11.9 MWhT per year
– The vertical facade system consists of 39% transparent glass, and 61% insulated panels, with an overall U-value of 1W/m2K; the roof’s U-value is 0.181W/m2K